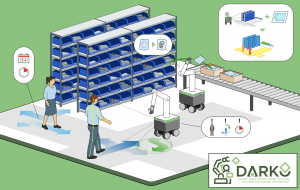
Agile production crucially depends on the effectivity of intralogistics processes. Robots as components of these processes have the potential to be a game changer — provided they are highly flexible, capable, cost- and energy-efficient, safe and able to operate in work environments shared with humans. However, the current state of the art falls short of providing these capabilities given the requirements for future production systems.
Thus, DARKO sets out to realize a new generation of agile production robots that have energy-efficient elastic actuators to execute highly dynamic motions; are able to operate safely within unknown, changing environments; are easy (cost-efficient) to deploy; have predictive planning capabilities to decide for most efficient actions while limiting associated risks; and are aware of humans and their intentions to smoothly and intuitively interact with them.
To maximise its impact, DARKO is aligned with use cases at the largest manufacturer of home appliances in Europe. It will demonstrate, in relevant scenarios, autonomous capabilities significantly beyond the current state of the art in dynamic manipulation (e.g., throwing of goods, picking and placing objects while in motion), perception, mapping, risk management, motion planning and human-robot interaction.
Beyond its impact through improved capabilities in these areas, DARKO will provide answers to the questions where and how dynamic manipulation should be integrated as the most efficient solution in intralogistics. Since arm manipulators can, in principle, display super-human performance in terms of accuracy and repeatability, the value of integrating dynamic manipulation, e.g. throwing, into transport processes may well exceed current expectations.
Objectives
DARKO has as its main overarching objective to research and innovate for efficient and safe intralogistics robots in agile production. These two aspects are reflected in the following objectives. These scientific objectives are aimed at realising the fundamental enabling technology that will make intralogistics in agile production flexible, robust and easily deployable.
Objective 1: Efficiency in manipulation
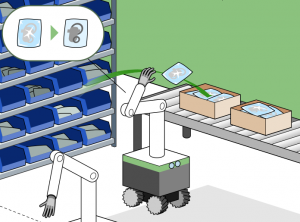
Static and quasi-static pick-and-place of objects, which is traditional in the industry, requires a reduction in velocity that reduces efficiency. Pick and place while in motion, is more efficient time-wise but comes with a wealth of challenges. It requires accurate control of the base and manipulator (with human-like performance) simultaneously to swipe the object in and out, while avoiding inadvertent collisions when humans are in the vicinity. Throwing objects, e.g. onto a conveyor belt, is also advantageous as it enables the robot to place objects outside the arm’s maximum kinematic range. This can also increase time efficiency compared to driving the robot to the desired location. DARKO aims to ease such dynamic manipulation tasks by exploiting inherently elastic manipulators, inertial coupling effects, flexible end-effectors and endow robots with the required high-speed perception. It further develops algorithms to increase efficiency and safety. To meet this objective, a) we plan to a design an inherently elastic mechatronic arm and a compliant gripper, novel controllers with the capability of fully exploiting store/release energy mechanism b) develop real-time pick and place and obstacle avoidance mechanisms for the base and manipulator, c) dynamic model of object’s dynamics for throwing.
Objective 2: Efficiency in human–robot co-production
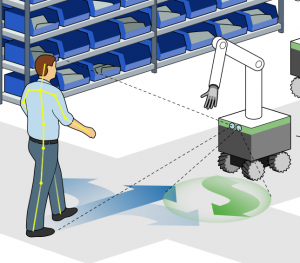
We will increase efficiency and safety in environments shared between robots and humans in particular by means of learning and exploiting activity patterns, prediction and mutual communication of intents, as well as a novel framework for risk-aware planning and coordination. This will support predictive planning of activities to ensure zero-risk of collision.
We postulate that in order for intralogistics robots to be efficient, they must co-exist with human staff. Rather than building new fully automated warehouses, end users of all scales (from SMEs to international corporations) require smart automation that can effortlessly integrate with current warehouse facilities and, for the foreseeable future, efficiently interact with human workers.
By learning the typical motion and activity patterns, and using them in motion planning and scheduling, robots will be able to plan, and also execute their planned tasks and trajectories, more efficiently. We will substantially extend our previous work on human detection, tracking, and motion prediction, as well as spatial augmented reality for communicating robot intent. Underlying this work will be extended context-aware representations for human–robot spatial interaction (HRSI), and using them in causal reasoning for inherently safe and efficient HRSI.
Objective 3: Efficient deployment
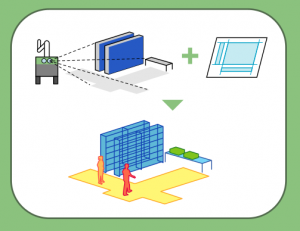
One of the main barriers to market of intralogistics robots today is deployment effort. Ease of deployment (low effort & high flexibility) is consistently listed as a top priority of industry stakeholders. We will address the objective of efficient deployment in particular from the point of view of failure-aware and failure-resilient mapping and localisation, as well as “auto-completion” of robot maps and information transfer using map priors from heterogeneous sources. Semantic 3D scene understanding typically requires large amounts of labelled training data, and use-case specific data sets are difficult to acquire. This makes data-efficient methods particularly important, and we will develop semi-supervised and self-supervised perception methods to reduce semantic annotation effort; which will in turn contribute to better-informed localisation algorithms.
Objective 4: Risk-aware operation for safety and efficiency
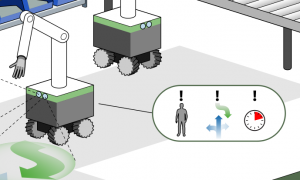
Efficiency and safety in intralogistics robotics can be achieved only by including risk assessment as a driving principle for the decisions taken by one or more intelligent agents acting at shop floor level, and must be done not only locally (through decentralised risk-aware intelligence) but also globally, guaranteeing that the overall orchestrated behaviour of robots, humans and machines takes explicitly into account the probability associated to different types of risk; e.g., strain on the robot hardware, failing to meet mission criteria, as well as human safety.
Aiming at this comprehensive risk awareness and minimisation, DARKO proposes to implement a functionally horizontal risk management layer, capable of gathering risk-related data from multiple sources, exploiting it to train corresponding predictive models, and using them to track and adjust robot trajectories within a so-called risk space. Endowing the cognitive mechatronic system with this capability to assess and anticipate the probability of an undesired event to happen facilitates much more robust behavioural management; both off-line, when scheduling the operational tasks,and on-line, by continuous planning and control of the robot actions.
Objective 5: Demonstrate feasibility in an integrated system
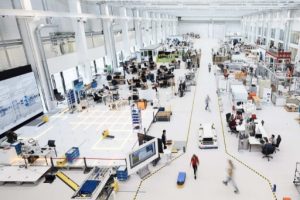
In addition to the achievement of its scientific objectives, DARKO also aims to demonstrate the feasibility of its efficient and safe intralogistics system for agile production in a realistic setting. The scientific objectives can only be fully effective and reach the desired impact if they are also combined and demonstrated in an integrated system in a realistic setting.
To this end, we will construct a permanent demonstrator at the ARENA2036 research campus, which will be a replica of a use case combined from real-world requirements of end-users associated with the consortium.
Work packages
More concretely, the work in the project is arranged in the following work packages:
- WP1: Efficient Mobile Dynamic Manipulation Platform
- WP2: 3D Perception and Scene Understanding
- WP3: Multimodal Mapping and Safe Localization
- WP4: Efficient and Safe Dynamic Manipulation
- WP5: Human-Robot Spatial Interaction
- WP6: Predictive and Safe Motion Planning
- WP7: Risk Representation and Operations Scheduling
- WP8: Requirements and Evaluation
- WP9: Management
- WP10: Dissemination and Exploitation
- WP11: Ethics